20/04/2023
Il progetto AGILE: intervista a Diego BassetIl progetto promuove la piena integrazione e digitalizzazione di discipline e funzioni aziendali, eliminando barriere di spazio, tempo e informazioni tra i diversi dipartimenti interni o nei confronti di fornitori esterni e partner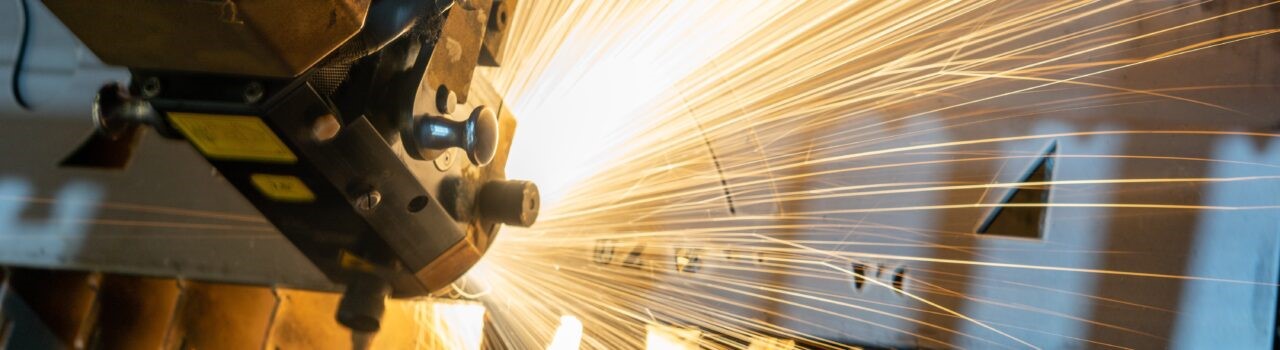
Quali sono stati i principali output del progetto?
Il progetto rientra in una filosofia di supporto alle iniziative di R&D delle industrie venete, con lo scopo di arrivare a soluzioni che possano avere delle ricadute ampie soprattutto nel tessuto regionale. Nella fattispecie poi, eravamo in piena pandemia, anche con una particolare attenzione alla possibilità di riadattare le strategie industriali a fronte di stress esterni come appunto un evento pandamico. La RIR M3Net nello specifico ha partecipato con due casi su due diverse linee di progetto: AM Teknostampi all’interno della linea “Prodotti di Fonderia” e Delka per la linea “Prodotti Saldati e Assemblati”. Il progetto è stato portato a termine con successo con il raggiungimento di tutti gli obiettivi tecnci e di ricaduta industriale prefissati. In particolare, per la linea “Prodotti di fonderia” è stato svolto un interessante lavoro comparativo che, basandosi su una strategia per la riduzione dei tempi di fermo macchina, ha messo a confronto dei tasselli realizzati con tecnologia tradizionale, fresando un pezzo di acciaio dal pieno e uno realizzato con innovative tecnologie di stampa 3D per materiali metallici avanzati. Sono state valutate le prestazioni di entrambe le soluzioni per poterne prevedere il comportamento e gli eventuali benefici.
Si è partiti da una criticità della produzione di un particolare componente per pressofusione di magnesio. Un processo nel quale il magnesio fuso viene spinto all’interno di uno stampo di acciaio del quale assume la forma e, una volta raffreddato, viene estratto il pezzo solido. Il componente in questione, a causa della sua forma particolare dovuta a esigenze tecnologiche, creava una forte usura in alcuni punti dello stampo in acciaio. Questo si traduceva nella necessità di fermare la produzione con frequenza maggiore rispetto al solito, smontare lo stampo per poterlo ripristinare prima di poterlo rimontare e avviare nuovamente la produzione. Queste operazioni portano ovviamente a importanti spese di tempo. All’interno della cornice del progetto è stato eseguito uno studio per poter ridurre significativamente i tempi di fermo macchina sostituendo la parte di stampo che tendeva a usurarsi con più frequenza con un tassello removibile. Questa strategia permette di ridurre i tempi di sostituzione dello stampo perché consente di estrarre solo una porzione di dimensioni ridotta e molto più facile da maneggiare (gli stampi in acciaio infatti possono arrivare a pesare anche diverse centinaia di kg) e di sostituirlo in tempi rapidi con uno di ricambio, cosa che non sarebbe pensabile fare con l’intero stampo per via degli alti costi di questo tipo di attrezzatura.
In questo caso i lavori hanno permesso di dimezzare i tempi per il cambio dello stampo, aumentare il ciclo di vita di ogni stampo con una diminuzione delle perturbazioni produttive facilitando quindi il rispetto della pianificazione della produzione. È aumentata l’efficienza grazie alla manutenzione molto più rapida dei tasselli la cui vita, che è determinata dalla resistenza all’usura, è stata allungata grazie alle nuove tecnologie utilizzate. Il caso presentato da Delka invece, afferente alla linea “Prodotti Saldati e Assemblati”, è basato sulla volontà di ridurre i tempi di riconfigurazione di una linea produttiva, in particolare di una stazione di saldatura. Questo aspetto, che ha una valenza di utilità autonoma, ha voluto evidenziare come in generale la riduzione del tempo di setup renda molto più flessibile ed economicamente accettabile il cambio di lavorazioni all’interno di un percorso produttivo standardizzato.
Per costruire il cuore di una stufa a pellet, cioè la struttura che conterrà il braciere e quindi la zona di combustione, Delka utilizza un innovativo sistema di saldatura robotizzato. Questo processo avviene posizionando i pezzi, i sotto-componenti, all’interno di una struttura che li mantiene nella giusta posizione reciproca e che permette al robot, sul quale è montata la torcia di saldatura, di compiere il percorso necessario a creare il cordone di materiale fuso che unirà i vari lembi. Tale struttura, detta maschera di saldatura, è stata al centro del lavoro svolto. Ogni modello di stufa richiede una maschera che sia progettata in modo specifico. La maschera viene poi fissata su di un supporto mobile che fa parte del robot e che si muove in sinergia con il braccio della torcia. La sostituzione di una maschera per poter realizzare un modello diverso comportava un notevole dispendio di tempo che poteva arrivare anche a 4h. Questo perché era necessario, oltre al fissaggio della nuova attrezzatura, anche la verifica dell’intero percorso di saldatura del robot ripristinando i vari riferimenti geometrici e spaziali. Il sistema messo a punto durante il progetto ha invece consentito di ridurre drasticamente questi tempi a circa 35min.
È stato poi studiato un sistema per l’archiviazione dei dati di saldatura digitalizzata che consente di sviluppare un meccanismo di individuazione di errori o difetti basato su eventuali incongruenze dei dati raccolti. Inoltre, è stata creata una procedura agile, in collaborazione con i partner di progetto, per l’ottimizzazione dei parametri di saldatura attuabile in gran parte da remoto per poter far fronte alla eventuale indisponibilità in sede del personale specializzato. Questo consente di adattare in tempi rapidi il processo all’utilizzo di nuovi materiali anche nel caso di indisponibilità di questi sul mercato come purtroppo è successo in varie occasioni in questi anni. In entrambi i casi i risultati sono stati in linea con le aspetattive e con le esigenze per cui era sorto questo progetto che è nato nel pieno periodo pandemico come risposta del tessuto industriale veneto alle nuove sfide che l’emergneza aveva posto.
Rispetto ai progetti precedenti, in questa occasione la Regione ha imposto una collaborazione tra più reti. Come valuta questa novità?
Allargare le collaborazioni a più reti comporta inevitabilmente il mettere in comunicazione settori diversi. Questo porta certamente ad alcune sfide per la ricerca di punti e processi comuni o di tecnologie e skills trasferibili. Queste, come tutte le sfide, nascondono numerose opportunità che nascono dai nuovi stimoli e dalle possibilità di applicare tecniche, più o meno consolidate in un settore, in un modo innovativo risolvendo magari criticità in un altro. La contaminazione tra settori, se svolta in modo costruttivo e con la capacità di astrazione dei concetti alla base dei problemi o delle criticità di un certo comparto industriale, può certamente portare a un incremento accelerato di soluzioni con uno sviluppo incrociato delle competenze e delle conoscenze. Il progetto Agile con i suoi risultati ha mostrato proprio questo. I casi industriali proposti hanno visto una quota parte di lavori in sovrapposizione con soluzioni simili adottate per risolvere problemi peculiari di una singola azienda ma riconducibili a fenomeni comuni presenti anche in altre di altri settori. Questo ha consentito una notevole ottimizzazione delle risorse economiche portando anche al risparmio di tempo di setup, elemento fondamentale nella pronta risposta a situazioni emergenziali.
Il progetto ha favorito una reale azione di networking tra aziende e università? Sono stati coinvolti nuovi player?
Il progetto Agile è cominciato in una fase emergenziale, in una situazione ormai nota ma che all’epoca ha posto davanti a tutti delle enormi sfide e degli ostacoli difficilmente sormontabili con i mezzi ordinari. Primo tra questi è stato proprio il distanziamento. Il progetto è nato anche per far fronte a questo tipo di emergenza e sembra quasi un paradosso poter dire che sono proprio le relazioni tra i vari partecipanti che hanno permesso di poterlo realizzare con successo. Come in altri progetti, alcuni partner hanno portato il loro contributo fornendo il loro know-how o le loro tecnologie, altri fornendo un problema da risolvere assieme all’idea generale per farlo. Questo ha portato a un proficuo scambio di informazioni e alla realizzazione di nuovi percorsi per ottenere i risultati tangibili che sono stati il vero successo del progetto Agile. Non sono mancate le difficoltà: un progetto di questo tipo, che ha coinvolto in modo trasversale aziende operanti in vari settori e diversi dipartimenti dell’università, porta sempre con sé alcune criticità nella gestione dei task e nella collaborazione con delle tempistiche che potessero conciliarsi con le attività ordinarie. È stato però appagante vedere come le entità con maggiore esperienza nel campo dei progetti finanziati, e tra queste sicuramente quelle di estrazione accademica, abbiano saputo coinvolgere anche chi ne aveva meno o partecipava a questo tipo di lavori per la prima volta.
Le Reti Innovative Regionali hanno superato la fase di avviamento e si stanno sempre più consolidando. Stanno realmente supportando le sinergie Università-Impresa? Dal suo osservatorio ritiene che vi sia un processo di maggiore consapevolezza delle imprese venete verso processi di Open Innovation? E, d’altra parte, come si sta evolvendo il ruolo dell’Università nei confronti della terza missione?
Le rir hanno sicuramente scavallato il primo ostacolo e cioè quello di farsi conoscere come entità facilitatrici nella realizzazione di progetti congiunti con ricaduta industriale a livello regionale (e non solo). Sicuramente i momenti più efficaci per la sinergia tra soggetti coinvolti nell’innovazione sono i progetti congiunti. È abbastanza intuitivo che un progetto strutturato, con degli obbiettivi scientifici ed economici chiari, con una suddivisione precisa di ruoli tra partner e che vede una significativa presenza delle attività svolte dalle università del territorio, sia un momento di aggregazione e di comunione di intenti che fa crescere e maturare i soggetti coinvolti. Il concetto dell’Open Innovation è già presente nelle imprese innovative del territorio, a prescindere dall’esistenza delle RIR, ma la possibilità di avere delle strutture di ‘facilitazione’ come appunto sono le RIR catalizza questo concetto. Anche il ruolo Universitario è cresciuto nell’ottica dell’interazione con il mondo imprenditoriale, ovviamente con Dipartimenti più portati, o semplicemente più vicini, alla comprensione delle necessità innovative del tessuto imprenditoriale e altri più distanti. Il perseguire gli obbiettivi della terza missione, per la maggior parte degli operatori universitari, non è più visto come una necessità dettata anche da spinte ministeriali, ma si è radicata una convinzione che l’innovazione non va solo fatta su argomenti accademicamente accattivanti ma vanno privilegiati quelli che portano (anche in tempi non lunghissimi) dei vantaggi alle imprese. O in sintesi su argomenti innovativi che ‘servono’ alle imprese.
Quali sono le strategie future della RIR? Quali saranno gli asset principali su cui si concentreranno i nuovi progetti?
La RIR M3Net ha come focus operativo l’innovazione all’interno del settore manifatturiero avanzato e del relativo indotto, un aspetto che ci pone al centro delle necessità di molte imprese operanti nel territorio veneto. Le strategie future dovranno contribuire al supporto di tali imprese al fine di incrementarne la conoscenza in ambito di processi e prodotti innovativi, con parole chiave come nuovi materiali anche compositi, manifattura additiva, micromeccanica, integrazione uomo-macchina, digitalizzazione e in generale tecnologie abilitanti.
Un messaggio alla Regione, che proprio quest’anno dovrà dare avvio ai nuovi bandi per le RIR.
I progetti congiunti, come si spiegava prima, sono il momento in cui meglio si forgia lo spirito di collaborazione tra settori industriali diversi e università. Sono quindi dei momenti in cui è importante sia possibile dare alle imprese quel supporto per ‘osare’ su soluzioni o argomenti che altrimenti potrebbero rimanere nel cassetto dei sogni, e alle Università quegli spunti, che devono essere condivisi anche dalle esigenze del mondo industriale, per focalizzare linee di innovazione ad ampia ricaduta. Il messaggio alla Regione è quindi quello di continuare a sostenere l’innovazione, anche attraverso le RIR, aiutando queste ultime ad essere sempre più quel catalizzatore che può favorire lo sviluppo di collaborazione inter-rir e soprattutto tra aziende e Università.
Con il contributo di Nicolò De Marchi, Delka Srl
Scopri il nostro approfondimento sul tema.
Allegati:
banner.jpg (91Kb)